SW-ABF Fully Automatic Packaging Machine Instructions Part III
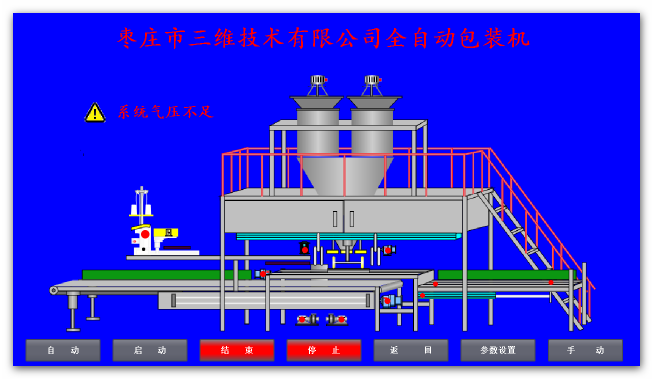
If there is an alarm information in the picture, after processing the alarm content and without alarm information, click the "automatic" button, or select the external knob. At this time, the "automatic" button is displayed as bright green, prompting the switch to be completed, press the instrument start button, start the weighing system, click the screen or external "start" button, the device starts after about 6 seconds of initialization, alarm. Light accompanied by sound and light alarm, prompting the relevant personnel equipment to start, bagging swing arm to perform a lifting and falling action to return to the ready position, bagging car if not in the ready position will return to the ready position. After the initialization is completed, the start button on the screen lights up and the device enters normal working state.
Downtime operation
There are two ways to stop the operation. One is to stop the operation directly by clicking the "stop" button on the screen or the external stop button. The device immediately stops the action being executed according to the stop command, and each drive solenoid valve loses power.
This shutdown mode is mainly used in debugging process or abnormal production state.
Another way is to click on the screen or the external end button. At this time, the instrument stops weighing. The instrument that has finished weighing stops after performing a feeding action, and the equipment enters the shutdown state after all the feeding is completed. This function is mainly used to prevent material storage in weighing silos or transitional silos when the work is completed or off duty, resulting in material scattering due to the loss of support due to material gravity of the valve after the compressor shutdown pressure decreases.
V. Maintenance
Maintenance regulations
1. Before each shift, add lubricant to the oil mist according to the regulations - ISOVG32 turbine oil (brand SMC, PMC pneumatic components allow no refueling, but once refueling, always refueling, no longer oil-free lubrication). And drain the sewage from the water separator side by side.
2. After each shift, all parts of the machine should be cleaned, especially the accumulated materials on electronic scales, sensors and other parts. Brush or compressed air cleaning is required.
3. Long-term shelving shall:
A. Clean up the accumulated material of the parts of the machine thoroughly.
B. Coating anti-rust oil on exposed parts of carbon steel.
C. Add grease to the moving parts.
D. Lock the moving parts.
E. Drying agent should be added to appropriate parts.
F. Covered plastic film.
G. The pneumatic system is started every 30 days.
4. The warehouse connected with the hopper must be cleaned thoroughly once a week, and the cleaning times of viscous materials should be increased, so as to avoid the lump of metering materials.
Inspection requirements
1. Whether there is any abnormal sound when the machine is running, if there is, the machine should be shut down and checked for elimination.
2. Special attention should be paid to the cylinder, which is the actuator of the machine.
3. Manual operation of solenoid valves should be performed when checking the performance of solenoid valves.
4. Adjust the working pressure of the relief valve to ~0.55PMa.
5. Adjust the oil mist adjusting screw to 1 drop per minute. When inspecting, white paper can be put in front of the muffler. After about 30 minutes, oil stains should be seen.
Repair
1. Before any maintenance work, the power supply must be cut off and the gas supply must be shut off.
2. Electrical appliances are repaired once in 500 hours.
3. Machinery is repaired once in 2000 hours.
4. According to the wear and tear of each component, the following components should be replaced after 107 discharges at most:
A. All solenoid valves.
B. All bearings and bearing shafts.
C. Output relay.
5. Replace worn parts and components in time according to the operation of each component (especially the replacement of cylinder piston).
Analysis and treatment of common faults:
Troubleshooting Method for Causes of Faults
A. When the feeding arc door works, it vibrates too much . The working position of the feeding arc door is not right ; Adjusting the position of the cylinder support and the connecting length of the connecting bolt
B. The one-way throttle valve does not work. Correctly adjusting the one-way throttle valve or replacing this part.
C. Buffer Valve at Bottom of Cylinder does not work . Regulating Needle Valve
When the bottom door of the barrel closes, the recovery signal of the bottom door of the barrel fails. 1. Check whether the position of the induction switch is correct, the measuring process has not started or replaced this piece, and the electricity supply.
Is the gas line in good contact?
The bottom door of the barrel closes inappropriately when the bottom door of the flushing barrel closes inadequately A. Correctly adjusting the one-way throttle valve material of the barrel cylinder, the weighing process can not normally carry out 11 barrel bottom door recovery signal failure B. Check whether the position of the induction switch is correct or not.
The primary feeding has exceeded the weighing range. 1. The material flow is too large. 1. Adjust the opening of hopper insert.
Executing Elements - Abnormal Cylinder Action a. Solenoid Valve Failure a. Replacement or Repair
B. Cylinder piston damage. B. Replacement of piston
C. insufficient compressed air pressure. C. increase supply pressure to ensure 0.5-0.6 MPa D. loosening of electrical circuit, poor contact D. repair, elimination
6. Operational Procedures
(一) Prepare for startup
1. Purge and sweep.
A. Purge the dust of sewing machine interior thread and the dust of sewing machine photoelectricity.
B. Clean the guide rail, the roller and the cylinders of the cart and remove the dust in the body. C. Detection of dust, especially bearings, cylinders and clamps, at the blowing-in and bag-clamping devices
Contact point.
D. Purge the dust on the working table, the manipulator and the cylinders of the bag-feeding machine as well as on the photoelectric emission. E. Purge the dust on the working table and photoelectric surface of the bag feeding device.
F. Cleaning the dust on the operating cabinet.
G. Purge all conveyors, especially bearing Hill dust on conveyors.
H. After sweeping, check whether there is any dust on the two photoelectric parts of the sewing machine and one set of photoelectric parts of the bag feeding machine. If there is any dust, blow it off again.
2. Lubrication
A. After the sewing machine is purged, a little white sewing machine oil (22 # sewing machine oil) is applied to the moving parts of the sewing machine with an oil gun. Oil is pumped every two hours during normal work.
B. Every three months, oil gun is used to feed the universal joint of the guide device, bag centralizer screw of bagging machine, gears in gear boxes everywhere, bearings with seat and sprocket chains everywhere with a little 2 # lithium grease.
C. Change the sewing machine white oil every six months.
3. Check
A. Check whether there are any bags on the bag feeder, and place bags according to the standard. The requirements for placing bags are as follows:
1. Packing bags should be placed neatly on the stacking warehouse of the bag feeder, that is, the bag mouth should be close to the side of the baffle and the right side of the bag should be close to the advancing plate.
2. The left side of the stack is 1-2 cm away from the side baffle of the upper bag machine.
3. Packing bags should meet the standards.
A. Check whether there is compressed air in all parts of the automatic packing line.
B. Check the switch positions on the operating box: "Single machine/interlock" should be in the interlock position.
4. Boot-up operation
Closed control system, motor drive and other control cabinet power supply, touch screen and instrument power on, touch screen into the welcome screen: click "Enter" into the operation screen.
Before startup, first of all, set and confirm the parameters. Click on the "Parameter Settings" button on the screen and enter the settings screen to set the running parameters.
Press the instrument startup button, start the weighing system, click the screen "automatic" button, or external knob selection, then the "automatic" button is displayed as bright green, prompting the completion of the switch, click the screen or external "start" button, the device starts after about 6 seconds of initialization, initialization is completed, the device enters the normal working state.
5. Shutdown operation
There are two ways to stop the operation. One is to stop the operation directly by clicking the "stop" button on the screen or the external stop button. The device immediately stops the action being executed according to the stop command, and each drive solenoid valve loses power.
This shutdown mode is mainly used in debugging process or abnormal production state.
Another way is to click on the screen or the external end button. At this time, the instrument stops weighing. The instrument that has finished weighing stops after performing a feeding action, and the equipment enters the shutdown state after all the feeding is completed.。
V. Maintenance and Maintenance
(一) Maintenance of functional components
1. Maintenance personnel or operators should observe whether the connecting parts of the moving parts are loosened. If loosened, they should tighten in time.
2. Maintenance personnel or operators should observe whether the speed of moving parts is normal in each shift. If the speed increases and vibration increases, they should observe whether the nut with valve joint is loosened in time. If it is loosened, it should be restored.
Tighten the nut after adjusting the speed. On the principle of cylinder speed adjustment, the speed should be slower in order to satisfy the action function, so as to prolong the life of cylinders and structural parts.
3. Maintenance personnel or operators should observe whether the position signal of magnetic switch is normal (generally look at the indicator light of magnetic switch).
(二) Maintenance of pneumatic control box
1. Maintenance personnel or operators should observe whether the gas control pipeline is broken or loosened, if it is solved in time.
2. Maintenance personnel or operators should observe whether the barometer values and oil drops are normal, and adjust them in time.
(三) Maintenance of automatic bag feeding device
1. Maintenance personnel or operators should observe whether the connecting parts of the moving parts are loosened. If loosened, they should tighten in time.
2. Maintenance personnel or operators should observe whether there is dust on the photoelectric switch and remove it in time.
6. Analysis and treatment of common faults:
1. The sewing machine is not tangential, while the bag-cutting 1 photoelectric switch has dust 1 dedusting.
The position of photoelectric switch is not correct 11. Re-adjust the position of photoelectric switch
2. The long cylinder of the bag collector does not move downward 1. Check the operating conditions of the cylinder of the bag collector.
A. Manual reversal to check whether the long cylinder and air passage are normal
B. Check whether the PLC has output signal
C. Check whether the connection of long cylinder solenoid valve is normal
3. No movement of the towing bag motor
A. Check the power supply of the frequency converter
B. Alarm of Inverter
C. Check whether the PLC has output signal
D. Conditions for checking in place
4. One side of the bag during forward delivery
A. Fine-tuning the position and angle of the front roller and synchronous pulley
B. Adjusting the Spacing of Bag Centering Frame and the Medium Speed
5. Low vacuum of two suckers
A. Cleaning Dust in Vacuum Filter
B. Check the air tightness of the whole pipeline and whether the sucker is damaged.
C. Clean the whole pipeline and blow away the dust inside.
D. Inspection of vacuum pumps (according to the instructions for vacuum pumps)
6. No movement of bag-feeding manipulator
A. Check the power supply of the frequency converter
B. Alarm of Inverter
C. Check whether the PLC has output signal
D. Conditions for checking in place
7. Packing Car No Packing A, Check Power Supply of Frequency Converter
B. Alarm of Inverter
C. Check whether the PLC has output signal
D. Conditions for checking in place
- Last:SW-ABF Fully Automatic Packaging Machine Instructions Part II
- Next:Zaozhuang Sunweigh was invited to attend the 6th Shanghai International Powder and Processi
【Related Product】
- Full-automatic Packaging Machin
- Semi-automatic valve bag packin
- Semi automatic powder packaging
- SW-ATF-180 Fully Automatic Pack
- Semi-automatic Ton bag Packing
- Double hopper granule packing m
- Single hopper packing machine
- Semi-automatic packing machine