Shandong Granular and Powdery Chemical Raw Materials Automatic Packaging Manipulator Pallet
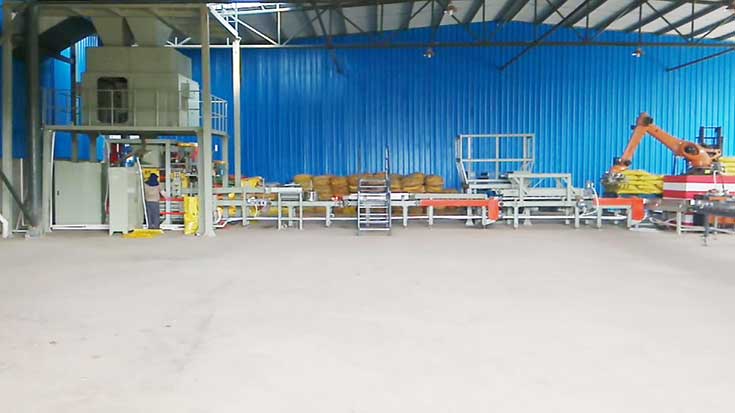
一、Composition of production line equipment of automatic packing manipulator palletizer for granular and powdery chemical raw materials:
The automatic packing manipulator palletizer production line can meet the requirements of weighing, bag feeding, bag taking, bag filling, clamping, hot-melt seam bag, rewinding shaping, weight detection, metal detection, removal, manipulator palletizer of 25kg granular and powdery chemical materials, and realize automation. The production line of automatic packing manipulator palletizer consists of quantitative electronic scale, bag feeding mechanism, bag feeding mechanism, bag filling mechanism, clamp shaping machine, dust removal, hot melt seam bag system, reverse charter machine, shaping machine, automatic weighing scale, metal detection machine, pick-up machine, manipulator palletizer, etc. Operation mode: automatic continuous operation.
1. Quantitative electronic scale
The feeding is in the form of spiral feeding and arc gate feeding controlled by cylinder, and the feeding is completed twice in the form of coarse feeding and fine feeding, respectively. Speed and accuracy are guaranteed. At the end of rough feeding, the cylinder controlled arc door will close the rough feeding outlet, and the fine feeding and air volume will be set by the remaining part of the fine feeding outlet. After the fine feeding, the feed outlet will be completely closed, and the whole feeding end. The weighing part adopts high rigidity barrel and frame, and the weighing sensor (original imported HBM series) is directly connected to the structure, which can improve the zero-return speed and static accuracy of the scale body.
The weighing control instrument adopts the most advanced original imported Canadian Gemmann instrument. It has 100 times/second high-speed A/D conversion and digital processing capability, and is equipped with BESSEL low-pass filter, which can effectively eliminate the impact caused by mechanical system vibration. The material of the contact part is 0Cr18Ni9, and the polishing of the contact part is more than 200 meshes.
2. Bag feeding mechanism
Bag feeding capacity: 800 bags/h, using two-bit automatic switching mode, motor-driven, to achieve the function of bag feeding and bag shifting. Two levels, the arrangement of bagging trays can store 200 empty bags (depending on the thickness of the bags). The contact material between the automatic bagging machine and the material is 0Cr18Ni9 with a polishing degree of 300.
When one stack of bags is exhausted, another stack of bags will automatically arrive at the position of picking up bags to ensure that there is no pause in loading bags. When you need to add pockets, an alarm will be given. When all the pockets are used up, the packaging opportunity will stop working automatically.
3. Bagging mechanism
Bagging capacity: 800 bags/h
Main features:
Vacuum suction bag, mechanical glove bag
(2) Bag Warehouse Shortage Alarm
(3) Alarm of insufficient pressure of compressed air
(4) Bagging detection and blowing function
The material in contact with the material is 0Cr18Ni9,300# abrasive polishing.
4. Clamp shaping machine
When the packing bag after filling material is laid down at the lower opening, it is held in the middle of the bag by the special processing bag-holding cart for powder material bags. The bag mouth is clamped and sent to the movable leading device. The movable leading device is connected with the hot-melt seam package system. After entering the sealing transmission chain, the bag mouth is guaranteed to be a zigzag shape, so that the bag can be controlled in the whole process. Adding a vacuum suction port near the inlet to absorb the dust from the bag mouth when it is clamped.
5. Dust removal system
High pressure spray cleaning is used to separate dust from dust-laden air. Centrifugal deposition is achieved through rounded shell. Dust-laden air can be purified through filter medium to meet the requirements of modern environmental protection. The equipment designs several suction points to suck and remove dust from material warehouse, packaging scale and lower entrance, so that there is no dust in packaging site. To environmental requirements.
6. SW-ASRS Manipulator Palletizer
SW-ASRS Manipulator Palletizer is composed of the main machine of the robot manipulator produced by German Kuka Company and the transit conveyor produced by the seller, the automatic bagging conveyor, the automatic pallet storehouse, the pallet conveyor, the pallet conveyor, the palletizing conveyor and the electric control cabinet. No manual operation is required on site. The whole set of palletizer realizes modular control. Touch screen is installed on the control panel, which can visually display the operation status of the palletizer. Operators can also choose manual operation according to the needs of the site, without any influence on the use of the whole system. Its main technical characteristics are as follows: pallet material: wood, steel, plastic or other composite materials (specific structure and material provided by users); palletizing mode: "2+3", "2*3" or other on-site palletizing mode; pallet lifting and lifting on pallet storehouse is realized by hydraulic station, equipped with pallet detection system, when there is no empty pallet in pallet storehouse, equipment will be issued. Audio-visual alarm prompts operators to place empty pallets, which can place 10-12 empty pallets at a time. The palletizing conveyor is composed of three stages of drag chain roller conveyor (the first two stages are powered, the last one is powerless, independent and interlocking with each other, to ensure the normal and stable operation of the equipment.
7. Integral Control System of Automatic Packing Manipulator Palletizer Production Line
The PLC uses Siemens, which can communicate with the host computer DCS and transmit data in real time. The control cabinet is equipped with touch screen and graphical display interface. By receiving the instrument signal, the packaging status of the current packaging machine and the statistics of the number of qualified and non-qualified products are displayed, and the operation status of the relevant equipment is displayed. The electric control cabinet is installed in the control room of the packaging workshop. It is equipped with indicator lights and operation buttons. It is used to operate the start-stop and status indication of packaging scale, conveyor, pouring bag, shaping machine, testing machine, automatic weighing scale and eliminating machine.
二、The main configuration of the automatic packing manipulator palletizer production line:
Cylinders and solenoid valves are made of foreign famous brand products Fisto and Siemens PLC, which have good reliability, high precision and long service life.
Technical parameters of automatic packing manipulator palletizer production line:
The packaging range of automatic packaging scale is 25kg, the packaging capacity is 400 packages per hour, the packaging bag is kraft paper bag, the sealing form is heat-seam package, and the packaging accuracy is (+0.1-0.2%) FS.
Manipulator palletizer maximum palletizing height: 2500_ (including pallet height), maximum palletizing weight: 2500KG (including pallet weight), normal speed: 1000 packs/hour (maximum speed: 1150 packs/hour).
- Last:Rizhao polypropylene factory purchased three-dimensional technology packaging machine in 20
- Next:Binzhou Starch Sugar and Crystalline Fructose Packaging Production Line
【Related Product】
- Full-automatic Packaging Machin
- Semi-automatic valve bag packin
- Semi automatic powder packaging
- SW-ATF-180 Fully Automatic Pack
- Semi-automatic Ton bag Packing
- Double hopper granule packing m
- Single hopper packing machine
- Semi-automatic packing machine